Proposed works
Proposed works
Reason for works
Albeit that this house is impressively airtight, it is highly ventilated and under insulated: conditions that recently resulted in mould in north-facing rooms. These rooms don’t benefit from the free heat of the sun. Its BER is G which is reflected in the fact that it’s hard to heat to a temperature of 20 °C in the main room and 18 °C elsewhere. The current owners accept lower temperature conditions but other occupants may not. Excluding the creation of a patio door in lieu of the current kitchen window, the proposed works are purely focused on energy efficiency and moisture management.
Owners’ comments
Despite the number of vents, one of the homeowners also said it didn’t feel like a draughty house, with the possible exception of the front bedroom (which happens to have the largest vent in the house – the open flue of the fireplace). The homeowner is considering blocking it temporarily with a chimney balloon to see if it reduces draughts and heat loss without giving rise to mouldy conditions again. It is quite possible that many homeowners who have less airtight homes try to compensate for draughts by turning the heat higher.
Due to a dry-eye condition, the owner is sensitive to how heat is delivered: her eyes dry out noticeably less with underfloor heating than with convector heaters and open fires. This was surprising as the first and last forms transfer heat primarily radiantly (heating solid bodies not the air in between), while a convector heater (in other words, a radiator) transfers 70-80% of heat through convection, thereby raising air temperature and lower relative humidity. Lower relative humidity can make the air feel drier. Perhaps the reason convector heaters and open fires contribute more to the owner’s dry-eye irritation is that they both result in large convection currents through the room and the air movement may cause further drying.
Design
The creation of the ‘major renovation’ standard has implications for what measures a homeowner of an existing dwelling (not listed on register of protected structures) may consider. In brief, renovating more than 25% of the surface area of an existing dwelling (where that includes some form of wall insulation) triggers the requirement for a cost-optimal improvement which is identified as 125 kWh/m2. See Section 2.3.1 and 2.3.2 of TGD-L:2018. Section 2.3.1 states “Where more than 25% of the surface area of the dwelling envelope undergoes renovation the energy performance of the whole building should be improved to Cost Optimal level in so far as this is technically, functionally and economically feasible.” For this 1940s mid-terrace, it means that wall insulation cannot be included in a minor renovation (or else it would immediately jump into ‘major renovation’ class and achieve 125 kWh/m2 per annum). An unusual byproduct of this is that in replacing the 68% efficient boiler, one should install (a) the highest-efficiency gas boiler (knowing that one is locking into relative high carbon emissions through burning fossil fuel) or (b) move over to electric heating and fit wall-mounted panel heaters and storage heaters in anticipation of a heat pump (knowing that the heat pump can’t be installed yet as the building fabric heat losses aren’t sufficiently high to render it financially viable). For a heat pump to be financially viable the heat loss indicator (HLI) as identified in in the Heat Loss Results tab of the DEAP software should be less than 2.0 W/K.m2. The shift to household heating using heat pumps is a key measure in Ireland’s transition to a low-carbon energy system.
On that basis, the proposed minor renovation fabric measures are new roof insulation, new windows and thermally retrofitting the existing doors. The services measures are a new gas boiler, new controls, low energy lights and completing the partially installed demand control ventilation system. In addition to the minor renovation measures, the proposed major renovation fabric measures are to insulate external walls, new insulated solid ground (with underfloor heating) floors and roof. The services measure is to install an air-to-water heat pump.
While external wall insulation can be a contentious choice of works in heritage terms, it is also increasingly common. Houses of 30 sqm per floor can scarcely afford to lose more space to internal wall insulation, yet externally insulating the two external walls can be carried out at a relatively low cost. While many standalone external wall insulation retrofits in older suburbs result in a loss of architectural detail and reduce the coherence of the streetscape, there are many examples of high-quality, architecturally-appropriate installations that are clearly compliant with planning regulations and in keeping with the original building and surrounding dwellings: only works of that quality are proposed here in a whole-terrace intervention.
Energy use, grants and tax relief
See Energy analysis below to understand the energy efficiency impact of the various works.
Proposed maintenance & energy-efficiency focused works
Upgrade Measures |
Minor renovation measures |
Major renovation measures |
---|---|---|
External works, ground levels, surface drainage |
N/A
|
N/A
|
Moisture-related maintenance work |
|
|
Re-pointing of mortar joints |
|
|
Re-rendering or plastering of walls |
|
|
Internal wall insulation |
|
|
External wall insulation |
|
✓ |
Cavity wall insulation |
N/A |
|
Fit flue damper or flue balloon |
✓ |
✓ |
Block flues |
|
✓ |
Window maintenance |
N/A |
N/A |
Secondary glazing |
|
|
Retrofit double glazing to external windows |
|
|
Windows & external door replacement |
|
✓ |
Draughtproofing |
✓ |
✓ |
High level of airtightness |
|
✓ |
Internal redecoration |
|
✓ |
Insulation of suspended timber ground floor |
N/A |
|
Replacement insulated solid concrete floor |
|
✓ |
Maintenance work to roof and drainage |
✓ |
✓ |
Roof insulation on flat ceiling |
✓ |
✓ |
Roof insulation on pitched ceiling |
✓ |
✓ |
Re-plumbing |
N/A |
|
New room heaters |
✓ |
✓ |
Heating system replacement |
✓ |
✓ |
Heating controls upgrade |
✓ |
✓ |
Domestic hot water storage upgrade |
N/A N/A |
N/A |
Solar hot water |
|
|
Re-wiring |
|
|
Change to 100% low energy lighting |
✓ |
✓ |
Standalone extract ventilation |
N/A |
|
Whole house demand control mechanical extract ventilation |
|
✓ |
Mechanical ventilation with heat recovery |
N/A |
|
Description of proposed minor renovation project and heritage impact
Item |
Description & comment |
Heritage Impact |
---|---|---|
Fit flue balloon |
Fit chimney balloon to bedroom flue |
None |
Draughtproofing |
Repair edge of attic hatch frame which allows air leakage (see air pressure results) |
None |
Clean gutters & moss off roof |
To facilitate roof ventilation & prevent water spillage or ingress clean the gutters. Moss growth on north-facing& roofs reduces ventilation under the roof tiles and may thus shorten the life of tile battens |
None |
Roof insulation on flat ceiling |
350mm Metac mineral wool, friction-fitted between joists and over. 0.10 U-value |
None |
Roof insulation on pitched ceiling |
Create 50mm ventilation zone over 75 mm mineral wool for depth of rafters. Fit PIR board (foil-face taped) below, counter-battens and plasterboard ceiling. 0.24 U-value |
Low Insulating below joists means installing new pitched ceiling at lower level (note: ceiling is plasterboard not plaster and lathe). Although the height of the pitched ceiling will be lower, no architectural features are removed |
Windows |
Replace existing single-glazed non-thermally broken windows (5.7 U-value) with Nordan Scandinavian pine windows 0.82 U-value, 0.37 G-value. |
|
Doors |
Thermally upgrade. The front and back doors are well-made with glazed vision panels over 2 solid panels. The simple square edges of the recessed panels suit retrofit works. Insulate the inside face of the two bottom panels with 2 layers of 9mm aerogel quilt and finish with 3mm ply & bolection moulding. Swop out single glazing in vision panel with slim-profile double glazing. The area-weighted U-value if goes from 2.72 to 1.24 W/sqmK. |
|
Wall-mounted radiators |
Remove under-sized vertical convector heater in kitchen and replace with properly-sized heater under the window, unless major renovation goes ahead |
None |
Heating system replacement |
Install new condensing combi-boiler (90.1% efficient in lieu of 68% efficient) for space heating and hot water. No secondary heating required due to size (in lieu of 30% efficient open fire). Remove cylinder. |
None |
Heating controls upgrade |
Time and temperature zone control and boiler interlock – two room stats, one on each floor, each with independent time control (level 3) |
None |
Whole house demand control mechanical extract ventilation |
Complete installation of ventilation system by fitting extract unit to kitchen ceiling connected to attic fan by ducts running through prefabricated housing fitted to kitchen ceiling, external wall insulation and cores in concrete eaves |
Moderate Housing from vent to core through outside wall in ceiling will be pre-finished and discrete. Using the correct equipment, there should be no risk of damage to eaves due to drilling. If required work is reversible |
Low energy lighting |
Fit 100% low-energy light bulbs. If recessed LED downlighters in top floor use rigid airtight hoods above sealed to plasterboard |
None |
Description of proposed major renovation project and heritage impact
Item |
Description & comment |
Heritage Impact |
---|---|---|
Block chimney stacks |
Having seen if mould returns after completion of ventilation system and use of chimney balloon for one heating season, insulate and block chimney flues and insulate and seal the larder grillage from inside |
Low Insulating flue with vermiculite is reversible. Fixed light-vent unit remains visible from outside |
Windows |
New aluminium-clad triple-glazed windows in optimum low thermal bridge position in external wall insulation. Fit patio door in lieu of kitchen window retaining existing lintel and structural opening width . Use sheep wool insulation filler fitted tightly by spatula into gaps between rear of window frame and masonry opening (in lieu of expanding foam). Fit proprietary airtight tapes to both sides of frame (to prevent air pressure difference being applied across this junction). |
None Original configuration of windows can be re-instated with high performance window by careful selection of window system |
External wall insulation |
EWI works proposed as part of a whole terrace thermal upgrade. External insulation, cills and innovative fitting of extract duct 0.27 = U-value
|
High EWI creates a step in the façade of terraced houses and can alter the depth of eaves and window reveals. The impact of this depends greatly on the recognition of the quality of existing architecture and its contribution to the streetscape, the quality of the design, the focus on quality and care of installation. |
Eaves Thermal bridge: aerogel |
|
|
Underfloor heating |
Given the owners’ strong preference for underfloor heating and intention to convert window to a patio door, the major renovation includes underfloor heating in lieu of relocating the wall heater. |
None - Low Original floor slab (breeze cement concrete) is poor quality. The slab and pebbles below are easy to remove to reach design depth for new insulated slab |
Heating |
Install air-to-water heat pump |
|
Additional comments
Cooker extract hoods should not be considered a normal or dependable extract ventilation system as their value is limited to the times when the occupant actually turns them on. It is recommended a humidity-triggered extract ventilation grille is installed in ceiling above the cooker extract hood.
The image shows chimney cowls of the case study house beside flue caps for de-commissioned flues. The design of the chimney cowls for the case study house is to aid smoke extraction and prevent bird nesting etc. They allow a minimal flow of air through. Note that the neighbour’s clay pots have had some temporary sealant applied to cracks. It is advisable that maintenance works be carried out on the chimney stack as soon as possible. The rear, southeast face of the Portland cement rendered stack is badly cracked and previous repairs with caulk have failed. The concrete flaunching (the stack’s concrete crown) needs to be re-laid or properly repaired soon as its exposed surface is quite badly cracked, increasing the risk of leakage. Several clay pots are cracked and may need to be replaced.
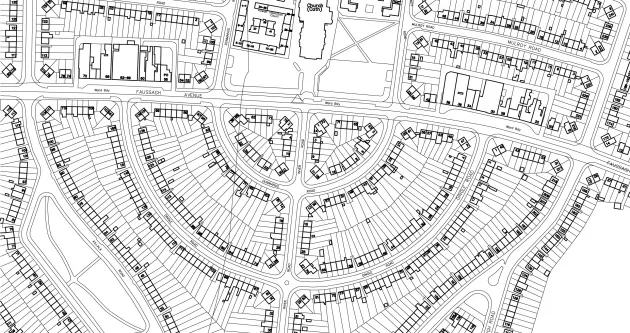