The works
The works
Completed maintenance & energy-efficiency focused works
Prevailing Upgrade Measures |
Done |
---|---|
External works, ground levels, surface drainage |
|
Moisture-related maintenance work |
✓ |
Re-pointing of mortar joints |
|
Re-rendering or plastering of walls |
|
Internal wall insulation |
✓ |
External wall insulation |
|
Cavity wall insulation |
|
Fit flue damper or flue balloon |
✓ |
Block flues |
|
Window maintenance |
|
Secondary glazing |
|
Retrofit double glazing to external windows |
✓ |
Windows & external door replacement |
|
Draughtproofing |
|
High level of airtightness |
|
Internal redecoration |
|
Insulation of suspended timber ground floor |
✓ |
Replacement insulated solid concrete floor |
✓ |
Maintenance work to roof and drainage |
|
Roof insulation on flat ceiling |
✓ |
Roof insulation on pitched ceiling |
|
Re-plumbing |
|
New room heaters |
|
Heating system replacement |
|
Heating controls upgrade |
✓ |
Domestic hot water storage upgrade |
✓ |
Solar hot water |
|
Re-wiring |
|
Change to 100% low energy lighting |
|
Standalone extract ventilation |
|
Whole house demand control mechanical extract ventilation |
|
Mechanical ventilation with heat recovery |
|
|
|
Description of completed upgrade project and heritage impact:
The following thermal improvements were carried out as part of the overall conservation works to the house:
Item |
Description & comment |
Heritage Impact |
---|---|---|
Insulation of timber floors |
The ground floor suspended floor was insulated and draughtproofed entirely from the underside via a substantial floor void with fibre insulation between the joists and breather membrane and mineral fibre boards fitted tightly to underside of joists below. The floorboards did not have to be raised and original significant skirting boards were unaffected. As such, there was no impact upon the original floor finish apart from lifting a minimal number of floorboards to provide access to each of the underfloor voids. The works had the secondary benefit of reducing air infiltration through a large area of floor. The original skirting was retained as it was an important historical feature of the house adding to the overall architectural character. |
None All original fabric was retained |
Insulation of solid floors |
The existing solid ground floor to the return was removed and replaced with an insulated concrete slab and underfloor heating. Perimeter insulation to the edge of the slab ensured that the floor insulation joined with the calcium silicate thermal lining to avoid cold bridging. |
Low Existing solid floors were not significant |
Internal wall insulation |
Given the relatively large heat loss wall area of the house (see Energy Assessment table above for more details), it was felt that walls should be upgraded where possible. As the walls of the return of the house had neither cornices nor significant wall features – and as the window reveals/weights boxes were adequately deep to accommodate a thermal lining board – it was judged acceptable to insulate these walls with 50mm of a proprietary calcium silicate board system. This application necessitated re-plastering the existing walls with a lime plaster to provide a plumb, even surface for the inflexible calcium silicate boards as the existing plaster was loose and uneven. Although the depth of the window reveals have now been changed, it was considered that there was sufficient thermal gain to justify the intervention. All solid walls contain moisture that may have originated as vapour from within the room or driving rain from outside. Brick-faced solid walls typically contain more water from driving rain than an externally rendered solid wall. The ideal insulation strategy for solid walls is one that ensures that energy is conserved within the room while the drying of the wall continues as close as possible to its original uninsulated state. However, by the act of insulating the wall from the heating system through the application of internal wall insulation, the wall becomes cooler and its relative humidity higher. Therefore, it is advisable to choose a wall insulant which is suitable for traditional single leaf walls which doesn’t hinder the ability of the wall to dry to inside and outside, such as the calcium silicate board used in this case study. This system is both vapour permeable and highly capillary active. However, its ability to “pull” water out of the wall is such that it is important that any leaks or damaged rainwater goods are repaired and that all cracks and mortar joints are in good repair to limit water uptake from the outside during driving rain. |
Low - Medium Although IWI was installed where no wall features existed, the lining has had a visual impact on the window reveals |
Attic Insulation |
The existing 100mm fibreglass attic quilt insulation to the return was topped up to a 300mm depth. |
None All original fabric was retained |
Retrofit double glazing of sashes |
Slim double-glazed units were fitted to all sash windows and weights adjusted (see Fig. 8-29). Although historic glass should be retained where possible, the owner, while being sensitive to the heritage value of the house, nevertheless had experienced icing of the glass over the winter of 2010/2011. Shutters for night-time insulation only originally featured in one room and historic glass survived in less than 40% of the sash windows. The Victorian sash frames (which were all retained) had single pane configurations and deep frames which facilitated retrofitting of the double-glazed units. Timber beadings were used instead of putty (see Fig. 8-30). There was also a concern that by improving the thermal efficiency of the walls, increased levels of condensation would occur to the single-glazed windows. Warm walls allow the desired temperature to be reached and to be held longer facilitating more moisture in the air and therefore more potential for condensation on colder surfaces such as single-glazed windows and uninsulated walls. It can be argued therefore that proper mechanical extract ventilation installed at the point of moisture generation (be that over the shower head, hob or washing machine) is even more important in traditional partly insulated houses than any other category of dwelling. Ideally these systems should be humidity-triggered to ensure that moisture is always managed. |
Medium - High Historic glass was removed. Double glazed unit is visible on close inspection |
Heating system upgrade |
The heating and hot water system was rationalized to increase the delivered energy. This was achieved by: • Relocating the existing gas boiler from an outhouse (with poorly insulated underground pipework) to within the building envelope • Increasing the pipe size and flow rate to the heating pipes to an appropriate level, lagging of pipework where absent and the introduction of a modern zoned control system. • Installation of a new hot water cylinder at attic level in an insulated enclosure (in this way it did not impact on the layout of the rooms). |
Low Existing service routes were used insofar as possible. The new balanced flue outlet was located to the side wall of the return |
Rainwater goods repair |
Joints of existing PVC downpipes to the return that were leaking were sealed. Leaking downpipes will increase moisture in solid brick walls and heat loss is increased when a solid wall is damp. |
None
|
Rendered plinth replacement |
Loose cement render to the plinth base of the external walls was replaced with breathable NHL hydraulic lime render to reduce the moisture content and improve the thermal efficiency of external walls. It is important that rainwater goods and façade finishes are maintained to keep external walls as dry as possible. |
None The modern cement plinth was unsuitable for the house |
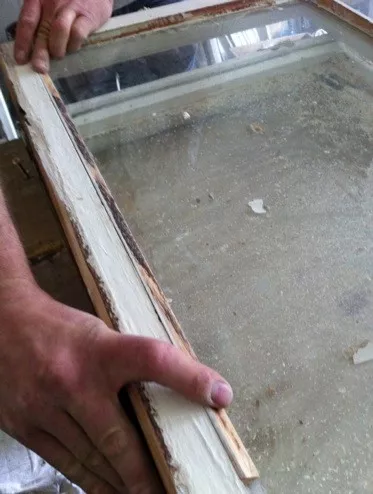
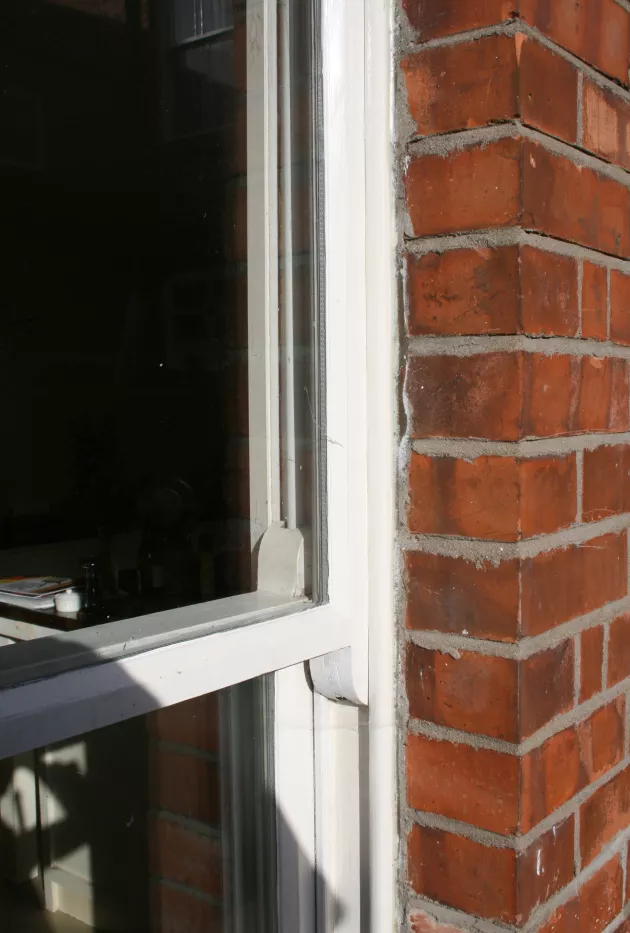
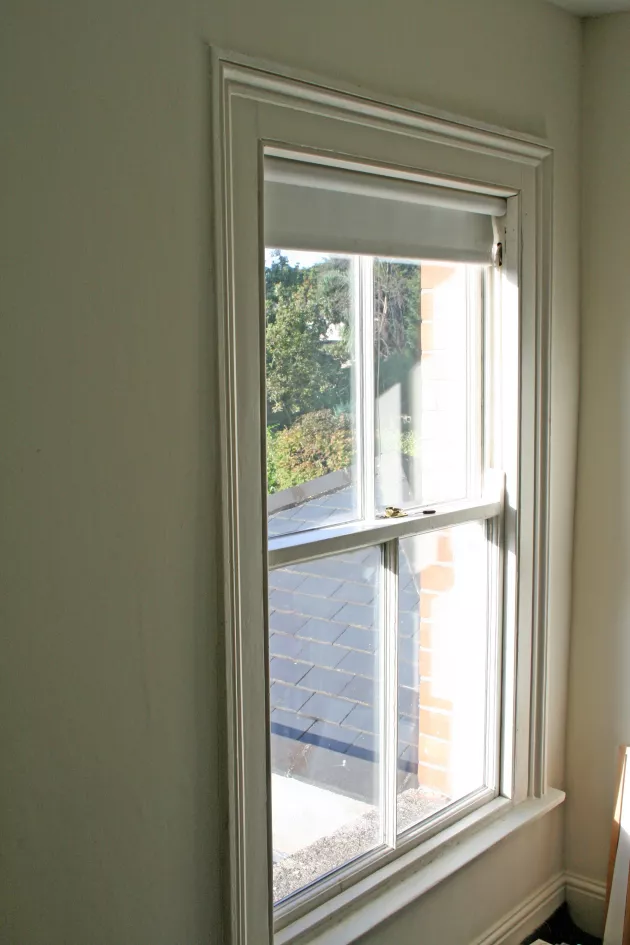
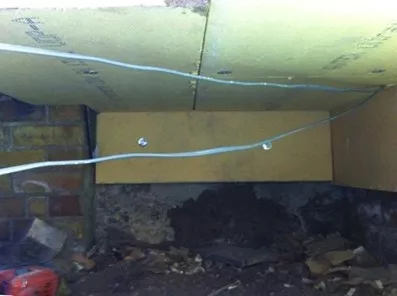
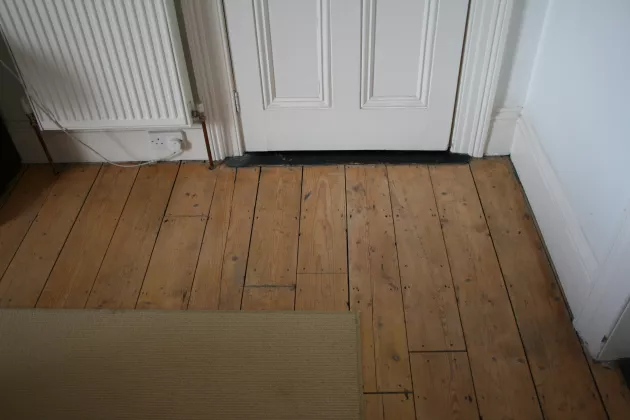
Possible future works
The owner intends to address draught issues with the front letterbox and is considering secondary glazing to the fixed stained glass sidelights of the door. Further work to the front living room is seen as a long-term consideration and will involve more invasive wall linings and opening up work to the bay window. Concern was raised in relation to the visual impact of the calcium silicate board on cornices even where a proprietary tapered board could be used to absorb the different thicknesses between the underside of the cornice and the insulation board.
Maintenance in relation to energy efficiency was seen by the owner as being more important in certain areas. Older window draughtproofing brushes have recently become loose resulting in perceptible draughts. The breathable casein distemper paint finish selected for the calcium silicate board and plaster finish is proving to mark easily and will require ongoing maintenance.
Cost of works
The item costs of the main retrofit measures is summarized as follows:
Retrofit Measure |
Before/After Performance (U value W/m2K) |
Cost (incl VAT @ 13.5%) |
---|---|---|
Insulate suspended timber floor 58m2 |
0.65 / 0.17 |
€3,700 |
New ground floor underfloor insulated slab to return 38m2 |
0.73 / 0.15 |
€9,400 |
Retrofit slim double glazing to existing sashes (14 windows) |
4.8 / 2.5 |
€9,000 |
Calcitherm Lining to walls of return 60m2 |
2.1 / 0.81 |
€13,250 |
Relocate boiler internally, new DHW cylinder & controls |
N/A |
€2,900 |