Building description
Building description
Composition
The case study house on Lennox Street is a terraced, two-bay, two-storey over basement late Georgian townhouse built c.1837. It retains an original two-storey return. The garden level basement to the rear has been substantially modified. The façade is laid in Flemish bond tan brick over the basement which is rendered to the front. Window openings feature flat brick arches with patent cement reveals and granite cills.
The entrance doorcase is typical of late Georgian - early Victorian houses in Dublin featuring a segmental fanlight (with glazing bars in a distorted petal design) over a simple entablature supported on scrolls from which narrow fielded panels extend downwards on either side of the doorset. The doorcase and fanlight are framed by a rendered reveal. The entrance doorleaf features a pattern of four raised and fielded panels.
The building and curtilage is on Dublin City Council’s list of protected structures.
Interior as built
The entrance hall is axial to the stair hall located to the rear and gives access to one-bay front and rear reception rooms. Unlike the North Great George’s Street case study – where both halls are the same width – the entrance hall in the Lennox Street case study is narrower, thereby allowing a large front reception room on this narrower plot. The first floor is laid out as a “two-room plan” with a two-bay bedroom to the full width of the front of the house and a one-bay bedroom to the rear. The original stair hall rises from basement to first floor level with return stairs giving access to the garden level family room and first-floor bathroom.
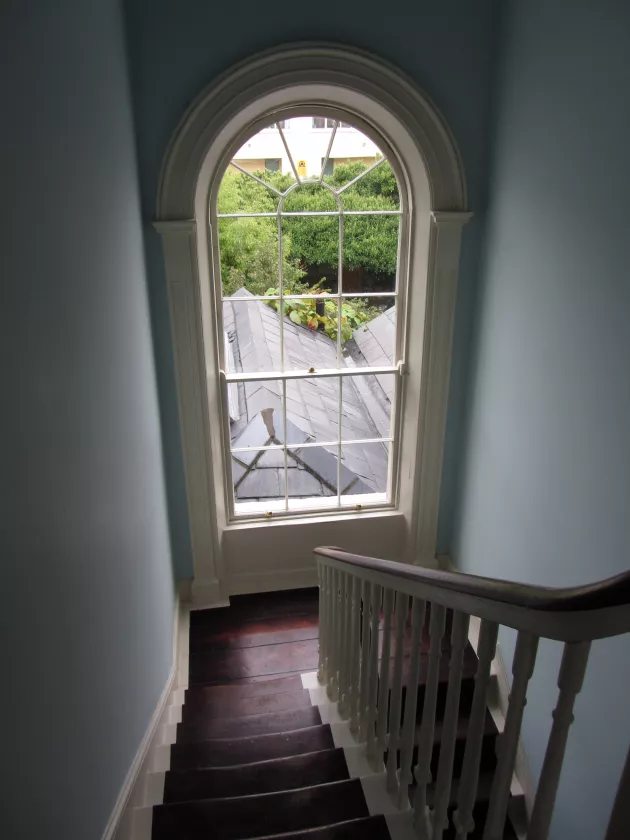
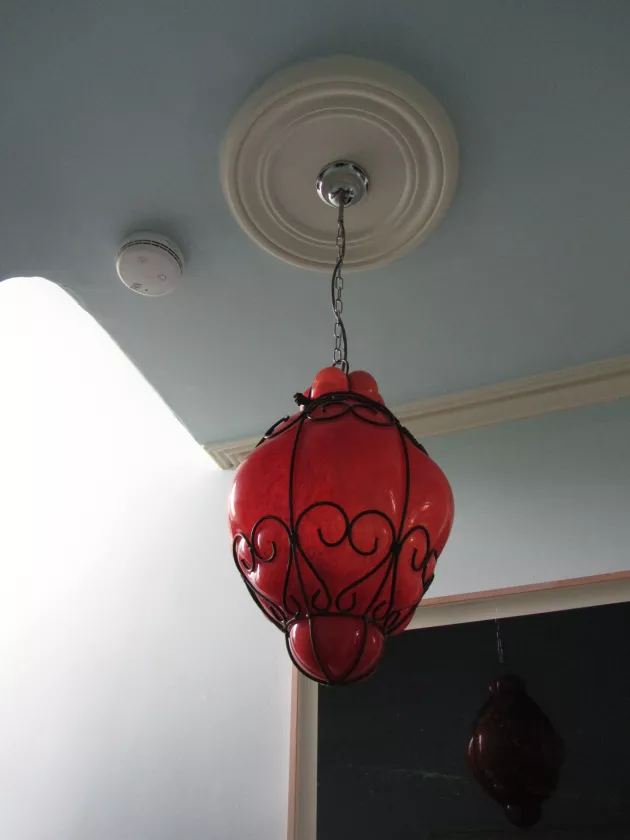
It is unclear if the plain-run running cornices are original or not. Several ceiling roses are new. While the cast-iron fire places in several rooms are historic and appear to be original, the marble fire surrounds and mantle appear to be modern. Many other interior features on the ground and first floor are intact, including window surrounds (including elegant fluted spandrels above shutter boxes), doors, architraves, floorboards and cut-string staircase. The basement and two return floors have the least amount of original fittings, having been significantly altered.
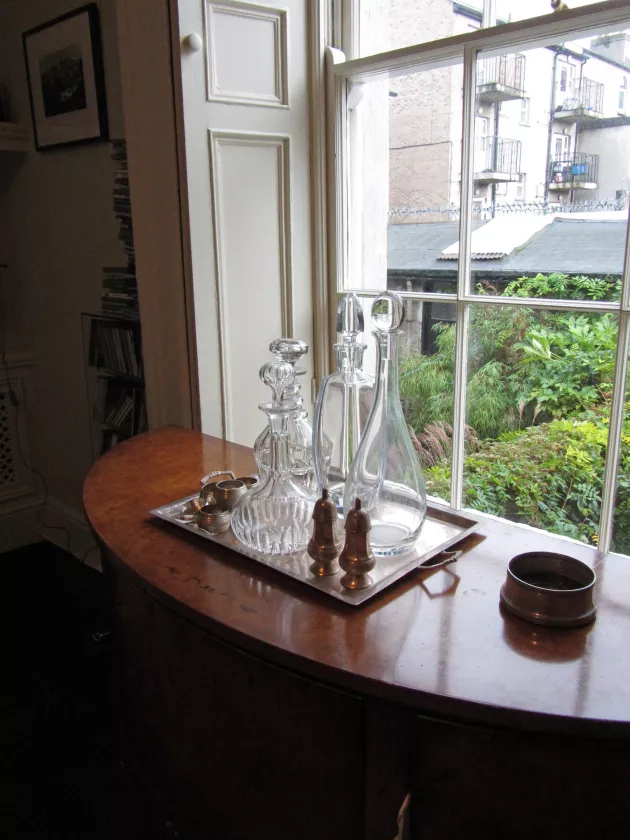
Comparing the photographs of the shutters open and closed one can see they can act as light excluders during the day as well as significant security devices. The value of traditional shutters from an energy efficiency perspective is examined elsewhere.
Changes since construction, existing condition
The owners purchased the property in 2007 and carried out significant maintenance and retrofit works before moving in. Interestingly, even though grants were available at the time for boiler and heating control upgrades, attic insulation and wall insulation, the owners did not apply, being too busy at work at the time.
At time of purchase, the dwelling had no central heating and heat was delivered via electric bar heaters in various rooms and a flame effect fire in the drawing room. The bathroom had an undersink heater.
Item |
Description & comment |
Heritage Impact |
---|---|---|
General |
It is hard to know how many original fittings have been removed from this house over time. Certainly, the internal decorative programme is simpler than the earlier and larger North Great George’s Street case study but also the contemporary Upper Leeson Street case study house |
Uncertain |
Cornices |
Unlike the Upper Leeson Street case study, this house has relatively simple running cornices only: is this evident of different budgets and specifications at the time, or that the cornices in this house were removed and replaced (for instance, after water damage occurred)? |
Uncertain |
Windows & shutters |
Historic glass replaced by clear float.
Re-conditioning of all shutters and sliding sash windows.
Re-fitting of ground floor windows (presumably after maintenance) to rear of house done without care: |
Low None Moderate |
Fireplace surrounds and mantlepiece |
It appears the originals have been replaced by modern polished marble pieces. Certainly, their proportions and detail do not seem to match the elegant cast-iron fire guards |
Moderate |
Basement level and lower return |
Significant changes made to install open-plan kitchen-breakfast room, wide opening made in external walls of rear of house and return facing garden |
Moderate – High |
Services |
Recent installation of central heating, rewiring, replumbing |
Low – high |
Windows and shutters
The owners had the shutters and sliding sash windows re-conditioned at a cost of ~€25K. They have intentionally omitted curtains to the front of the house and use the re-conditioned window shutters on ground and first floors instead for privacy and heat retention. The owners appreciate how the shutters don’t give a total ‘black-out’. They identified the tall round-headed window on the return as an air infiltration source: the weight of the upper sash is such that it always drops slightly from the fully closed position.
Decorative heater covers
One-and-a-half years after moving in, the owners fitted high-quality screens of fretted metal and timber around the convector heaters. The owner correctly surmised that the screens reduce the efficiency of the convector heaters and commented ‘but they look better, it’s a sacrifice that had to be made’.
Reportedly, screens that fully enclose a wall-mounted heater can reduce heat output by as much as 30%. Simple design principles would prevent most of that loss. Therefore, while aesthetics are important, the question of whether to install a screen at all – and the design, construction and performance of those that are installed – deserve significant attention.
Chimneys & flues
Air leakage in buildings of any age can cause a great deal of discomfort and add significantly to fuel bills. The flues are large – roughly square – and appear to have been lined in plaster (pre-dating the pre-cast clay pots of the Victorian period). Peering upwards within the fireplace recess, one can see a glimmer of daylight above. It is highly likely that a good proportion of the air sucked in at the hall door is pulled up the chimney stacks of this mid-terrace house.
As is common, only one of the fireplaces in the Lennox Street case study house is occasionally lit, but none of the flues have been closed or fitted with proprietary dampers. One has had mineral wool pushed into it – a crude but broadly effective measure. Chapter 2 explores the significant, but often unintended, role that open chimneys play in extracting large volumes of air and discusses how they can be restricted or blocked when appropriate.
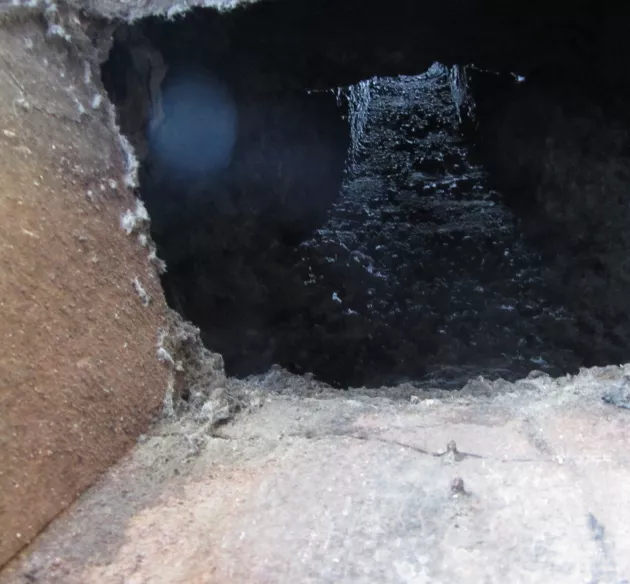
Air leakage, draughtproofing & insulation
The Q50 value for the airtightness test in this house was 10.29 m3/m2.hr. The default value for any dwelling in the DEAP software (for BER assessment) is 10.00 and for new dwellings in Technical Guidance Document L:2011 – Conservation of Fuel and Energy is 7.00. The measured value may therefore seem broadly acceptable, considering the house’s large size and open chimney stacks, but it becomes less acceptable when one considers that the house has relatively small surface area for the volume enclosed given its mid-terrace location and considering chimney stacks are sealed during such airtightness tests.
See section with key findings of the Airtightness Tests at various case study houses [link to follow], some are relevant to this house. The threshold of the hall door can be seen in the images accompanying this case study (from outside and inside). The owners are aware of a strong draught at the hall door in winter (to the extent that the hall can be bitterly cold when there’s snow). They intend to deal with this by fitting a heavy velvet curtain that would reach the floor: a quite traditional and often effective response. Such curtains tend to block air paths and due to their bulk can radiate heat back to the room.
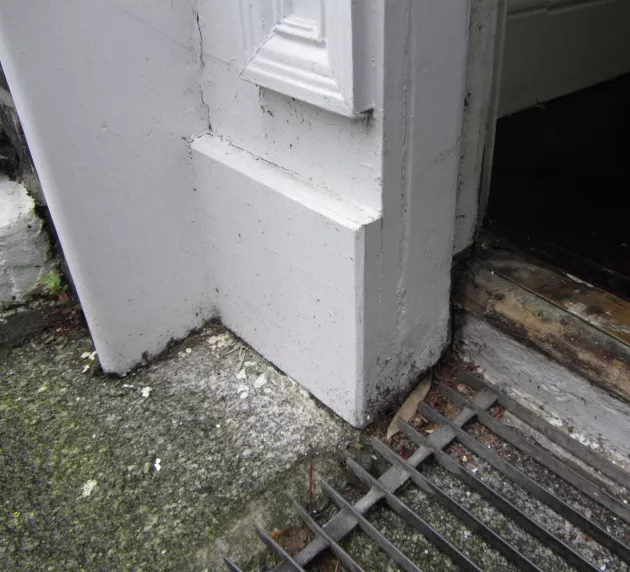
Examining the door, one can see that the brass strip at the base has clearly done a long service but does not provide an air seal and there are no compression seals along the rebated door frame. Fitting seals to the door should remove the primary cause of discomfort, ideally the line of seal (on all four sides of the door ope) should be continuous to prevent flanking air paths.
Surface-mounted compression seals are easily fitted and low cost but may be more visible than those inserted into new rebates. The fitter should ensure the seals have tight-fitting mitre joints (ideally bonded together) at upper corners of the door ope. At the base of the doorleaf, a drop seal could allow retention of the brass strip; alternatively, a wide range of airtight thresholds are available in mill finish aluminium, brass or gold finish for inward opening doors but will clearly require removal of the brass trip and be more visible. The drop seal requires removal of the door leaf for rebating and fitting. These seals only release when a trigger facing into the rebate on the hinged side is activated, i.e., at the moment the door closes.
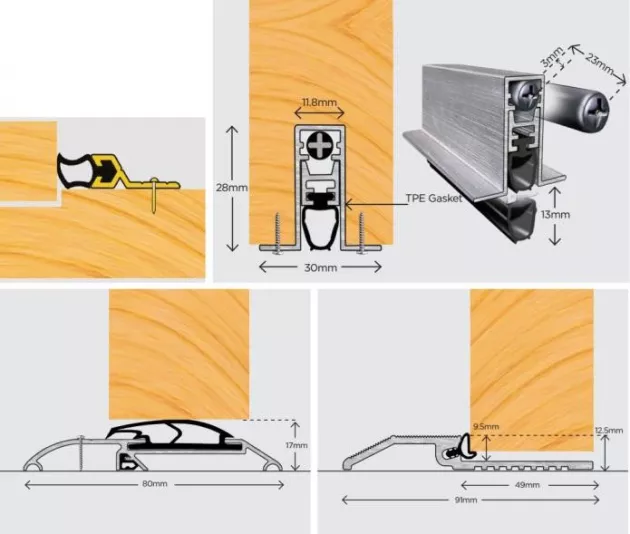
As can be seen in the image, a large gap is evident that could allow vermin or driving rain ingress, besides air infiltration. It appeared that this gap opened up during the window being re-fitted. Such a gap is easily filled by a conservation-focused maintenance operative.
Refer to the image where a crack in the timber panel that lines the shutter box void can be seen. Besides being an air infiltration point (on the air leakage path from the photo beside it), the panel is acting as the only ‘insulating’ element from inside to outside at this junction. The timber is fixed and painted into position to front but may be unpainted to rear (making that side vulnerable to changes in moisture content). It is likely that the panel has moved due to temperature and moisture differences and as the only movement possible is now the centre of panel it cracked. An aerogel ‘blanket’ (which is a highly insulating, thin and flexible quilt) could be fixed to the panel face without inhibiting the action of the shutters.
Control of moisture and bathrooms in warm pitched roofs
An all-too common condition is shown in one of the images: a large source of moisture – the shower head – without an extract ventilation grill above it. The water stains of condensed shower water can be seen in the pitched ceiling above. There is an intermittent fan in the bathroom but it is mounted in a wall 3.5m away at the far end of the room and several hundred millimetres below the apex of the ceiling. While this was the position that may have suited the builder best, the vent should have been located as near the room’s high point as possible (preferably ducting the moist air upwards and away). A fundamental principal that should be followed is that the point of extraction of moisture should be as close as possible to the point of moisture generation, unfortunately, commonly accessed guidance, such as the Homebond Manual, SR 54, or Technical Guidance Document F doesn’t give guidance on the location of extract ventilation.
Unfortunately, such ineffective installation happens regularly. The operatives who core walls are often employees of a general builder while a roofer may be a sub-contractor who may charge a day or half-day rate for carrying out this one task: a simple contractual and cost issue that may explain a lot of vent positions.
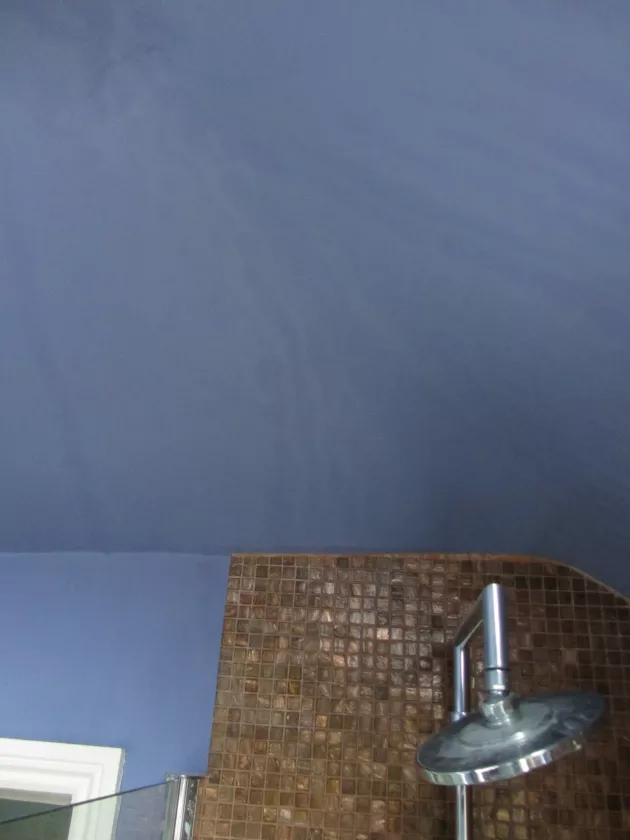
One should bear in mind that the ceiling of this bathroom is highly vapour permeable. If a vapour control layer were not installed above it, some moisture moves through it during and after each shower: in time, this vapour, which will condense on reaching the dewpoint, can degrade the insulants and hygrothermally stress the structure of the narrow thermal envelope of this pitched roof assembly. Where an insulant is hygroscopic, it can absorb vapour before 100% RH, thereby providing some buffering capacity and potentially reducing the hygrothermal stress of the timber structure. Plasterboard is 65% porous and has a vapour diffusion thickness of Sd = 0.1m, which means that vapour moves through it with the same ease it moves through 100mm of a stagnant body of air. Mineral paint that coats the plasterboard can have an Sd value of 0.04m (i.e., 40mm) depending on thickness: in contrast a vapour-retarding membrane has an Sd value from 1.0m – 200m and vapour barriers can have Sd value of >1,500m. Moisture should be managed passively through careful specification, as well as actively through properly designed and commissions ventilation.
Roofs with pitched ceilings (whether lean-to roofs or ‘cathedral’ ceilings) are more complex to build, insulate and ventilate than pitched roofs which have flat ceilings, or indeed flat roof structures. Recessed downlighters are particularly problematic in roofs with pitched ceilings creating thermal bridges (due to lack of insulation at light position) and potentially thermal bypasses (due to air path through light fixture to underside of breather membrane or even to slates above) are common outcomes. For more information, see on Ventilation and an exploration of how roofs are insulated and how under-performance can be prevented in warm-pitched roofs [link to follow].
Context
The dwelling was built as the second house in a four-house terrace development at the centre of the late Georgian expansion in land between the new southern ring road of Harrington Street and South Circular Road and Portobello harbour on the Grand Canal. These houses had much the same construction as the grander four-storey over basements townhouses built a generation before, with features such as basements and railed areas, sliding sash windows with shutter boxes, parapet roof with double apex roofs, but are more modest in aspiration and budget. The reduced number of floors is very clear (from the classic four storeys over basement), while the reduction of floor-to-ceiling heights within is signalled to the street by the more modest fanlight.
As the original composition and features of the terrace are still in good order, and as its original functional and architectural design was strikingly rational and visually pleasing, there is value in considering the composition of the terrace as a whole.
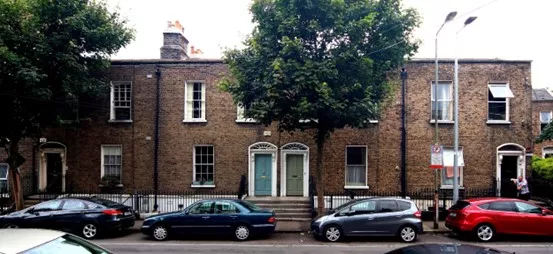
The internal plans are handled so that the doorcases of the second and third houses are grouped together at the centre of the terrace with common front steps; the first and fourth doorcases are at extreme ends. Front areas are enclosed by original wrought iron railings fixed into granite copings over rendered brick base walls. The continuous plinths and parapet frame the composition of the common façade. The rear elevation and return are finished in tan brick (those of the case study house are more recently re-pointed in cement). The rear returns are accessed by the central staircase aligned to the hall door. A semi-circular landing level arched timber sash window (above the roof of the return) lights the stairwell. Timber sash windows are retained throughout, some of which have had sashes replaced. No original historic glass is evident.
The main chimney stacks are grouped at the party walls separating the first and second, and third and fourth houses. The hoppers draining through the front parapet and associated downpipes have the same position. The terrace has two ranges of pitched roof. The front range is continuous: the rear range changes to hipped at centre so that the central valley drain can discharge through another valley gutter (over the spline wall that separates the second and third house) to the gutter of the continuous rear eaves. This is a more sensible and maintenance-friendly approach than found in some earlier Georgian terraces where water was drained from the central valley through the attic void to a parapet gutter via lead drain pipes laid at a slight fall: any leak would quickly result in inundation of the servants’ quarters.