Proposed works
Proposed works
Proposed maintenance & energy-efficiency focused works
Upgrade Measures |
Minor renovation project #1 |
Minor renovation project #2 |
---|---|---|
External works, ground levels, surface drainage |
|
|
Moisture-related maintenance work |
|
|
Re-pointing of mortar joints |
✓ |
✓ |
Re-rendering or plastering of walls |
|
|
Internal wall insulation |
|
✓ |
External wall insulation |
|
|
Cavity wall insulation |
|
|
Fit flue damper or flue balloon |
✓ |
✓ |
Block flues |
✓ |
✓ |
Window maintenance |
✓ |
✓ |
Secondary glazing |
|
✓ |
Retrofit double glazing to external windows |
|
|
Windows & external door replacement |
|
|
Draughtproofing |
✓ |
✓ |
High level of airtightness |
|
|
Internal redecoration |
|
|
Insulation of suspended timber ground floor |
|
|
Replacement insulated solid concrete floor |
|
|
Maintenance work to roof and drainage |
|
|
Roof insulation on flat ceiling |
✓ |
✓ |
Roof insulation on pitched ceiling |
✓ |
✓ |
Re-plumbing |
|
|
New room heaters |
|
✓ |
Heating system replacement |
|
✓ |
Heating controls upgrade |
✓ |
✓ |
Domestic hot water storage upgrade |
|
✓ |
Solar hot water |
|
|
Re-wiring |
|
|
Change to 100% low energy lighting |
✓ |
✓ |
Standalone extract ventilation |
✓ |
✓ |
Whole house demand control mechanical extract ventilation |
|
|
Mechanical ventilation with heat recovery |
|
|
Description of proposed renovation project #1 and heritage impact
Note: Planning Permission may be necessary for some or all of work proposed to this protected structure.
Item |
Description & comment |
Heritage Impact |
---|---|---|
Repoint façade |
Retain conservation craftspersons to repoint façade and if possible other brick elevations brick using wig pointing |
Positive
|
Reduce heat loss and draughts at hall door |
Fit seals at hall door to reduce draughts, and for added thermal value a heavy velvet curtain |
low |
Control air movement of stacks remaining in use |
Fit manual dampers to chimneys that are in use. These can be controlled by simple chain that is laid within the chimney pot for easy use of owner at hearth below (see Ch. 2.9.2) |
None |
Close, insulate & maintain stacks |
Insulate stacks that will not be used with perlite or vermiculite and close off chimney pots with proprietary lids that allows trickle ventilation (see Ch. 2.9.2). Ensure flaunching and chimney pots are in good order as water ingress afterwards will be harder to spot and will not be mitigated by drying effect of air passage.
|
None.
Positive Maintenance done with knowledge and care should always be welcome |
Background ventilation – extraction |
Fit the extract portion of a whole house ‘demand control’ mechanical extract ventilation (DC-MEV) system ensuring the extract grille is in optimum position in all wet rooms.
|
Low to medium On ground floor, especially front elevation |
Background ventilation – supply |
In rooms where wall vents can’t be fitted install sash locks to either side of frame so that the top sash is open ~5mm. This will ensure a reasonable background supply of air.
|
None |
Review maintenance of sliding sash windows |
Check the operations and seals of the sliding sash windows. Carry out maintenance work on the large arched window on the return to ensure it closes.
|
None |
Attic works |
Re-insulate both attics installing 350mm of tightly fitted sheepswool. Fit access hatch with airtight seals for front attic.
|
Low |
Heating system |
Keep existing boiler and cylinder and raise level of heating controls from level 2 to 3
|
None |
Background ventilation strategy for a protected structure
Background ventilation provided by a functioning, fit-for-purpose supply and extract ventilation system is the best way to ensure good indoor air quality is maintained. Occupants are generally a poor judge of air quality and of course can’t modify the ventilation regime when absent. Opening a window in a room such as a bathroom does not necessarily result in moisture-laden air leaving by that window – indeed air may come in through that window and take the moist air further into the house to condense elsewhere. Cross ventilation, created by opening windows at the front and rear of the dwelling, is a good way to lower internal air temperatures quickly and to remove unwanted moisture – if a large number of people are present or the extract ventilation system is inadequate. However, if the desire is to remove moisture, but not cool the building fabric, the windows to front and rear should be closed after a short amount of time, for example five minutes should suffice.
From a heritage risk and planning perspective, installing a background ventilation supply air for this dwelling is difficult to do. Trickle vents should not be fitted in sash windows (and are poorly regarded by the authors in any case), while wall vents would require the coring of walls. The extract portion of a whole-house, demand control mechanical extract ventilation system (DC MEV) should be less contentious as ceiling vents directly over the source of moisture can be ducted to one or more centralised fans and extracted to a roof tile vent visually concealed by a parapet. Background supply air needs a bespoke solution.
Consider the options for supplying the background levels of ventilation needed without heritage loss:
- Start by identifying where supply vents can be fitted without heritage loss reduce the extent of the problem. Arguably, a wall vent could be fitted to the wall of a modern rear extension or could be fitted to the uncorniced ceiling of a simple bedroom. In both cases, planning would still be required due to the protected status.
- Relying on adventitious air leaks seems less and less acceptable. Where maintenance and fitting are done correctly, the proportion of air entering the dwelling in this way should reduce in any case.
- Chimney stacks don’t supply air; they extract it by design. As explored in the section on Chimneys [link to follow], the volume of air extracted this way can be many times what is desirable for indoor air quality resulting in much cold air ingress. The extraction of a stack is subject to its height and design, the direction and speed of wind outside and the air pressure difference between inside and outside. This natural extraction will ‘fight’ the much-needed extraction in the rooms where moisture is produced which could result in condensate being dumped on surfaces of a room far from the moisture source.
- The best alternative appears to be the use of an old technology: sash locks (see image). These small brass fittings can be fixed to either side of frame so that the top sash is open ~5mm. That width across the full width of a window this creates a reasonable background supply of air, albeit the supply will vary depending on wind speed and direction outside and where air pressure outside is lower than inside could allow air extraction rather than supply. Nonetheless in the context it seems the best option with greatest control and least heritage risk.
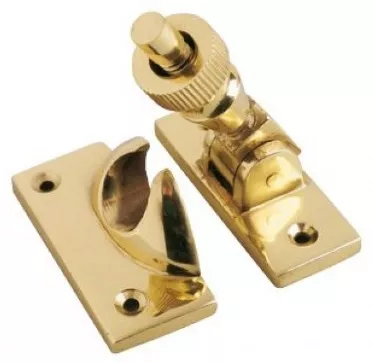
Description of proposed renovation project #2 and heritage impact
(These are in addition to, or in substitution of, various items in minor renovation project listed above: see summary of upgrade works). Note Planning Permission may be necessary for some or all of work proposed.
Item |
Description & comment |
Heritage Impact |
---|---|---|
Re-insulate the cathedral ceiling of bathroom on return |
Strip the bathroom ceiling and re-insulate. |
None |
Install IWI on walls of garden level basement and both floors of return |
Install fully-bonded, capillary open internal insulation to a maximum of U=0.50 W/m2K on exposed walls, ideally returning insulation on internal or party walls for one metre (U=0.70) to minimise thermal bridging |
Low |
improve airtightness of external walls of intermediate floors |
Lift floorboards to assess quality of workmanship at intermediate floors and improve what is found by installing wet plaster taped to joists (using proprietary airtightness tape |
Low |
Insulate panels of hall door |
Install two layers of (9 mm) aerogel quilt and 3mm plywood cover with timber beads to hall-side of recessed panels of hall door. |
Low This halves the heat loss of the door without heritage loss. The pattern of the beads replicate the pattern of the covered panels. |
Secondary glazing |
Fit secondary glazing to all single-glazed sash windows as per DCU case study in Chapter 2. |
Low |
Heating system |
In major renovation change to air source heat pump (ASHP) to avail of lower heating costs (for reasonably well-insulated and airtight dwellings) and thereby assist in decarbonising Ireland’s energy supply.
|
None |
wall-mounted heaters & insulate pipework |
Install over-sized wall-mounted heaters to suit the ASHP and take the opportunity to super-insulate all heating pipes to optimise efficiency: see Chapter 2.9.3. |
Low
|