The works
Completed maintenance & energy-efficiency focused work
Prevailing Upgrade Measures |
Done |
---|---|
External works, ground levels, surface drainage |
|
Moisture-related maintenance work |
|
Re-pointing of mortar joints |
|
Re-rendering or plastering of walls |
|
Internal wall insulation |
|
External wall insulation |
✓ |
Cavity wall insulation |
|
Fit flue damper or flue balloon |
|
Block flues |
|
Window maintenance |
|
Secondary glazing |
|
Retrofit double glazing to external windows |
|
Windows & external door replacement |
|
Draughtproofing |
|
High level of airtightness |
|
Internal redecoration |
|
Insulation of suspended timber ground floor |
|
Replacement insulated solid concrete floor |
|
Maintenance work to roof and drainage |
|
Roof insulation on flat ceiling |
|
Roof insulation on pitched ceiling |
✓ |
Re-plumbing |
|
New room heaters |
|
Heating system replacement |
|
Heating controls upgrade |
|
Domestic hot water storage upgrade |
|
Solar hot water |
|
Re-wiring |
|
Change to 100% low energy lighting |
|
Standalone extract ventilation |
|
Whole house demand control mechanical extract ventilation |
|
Mechanical ventilation with heat recovery |
|
Description of completed upgrade project and heritage impact
Item |
Description & comment |
Heritage Impact |
---|---|---|
External wall insulation |
Existing walls are reported to be of mass concrete construction with composite brick/block walls to the ground floor façade. The walls were insulated externally generally with 200mm expanded polystyrene. The owner wished to maximize insulation depths to get the greatest benefit from the retrofit. Dry dash render panels and plaster band features were accurately replicated to the front façade with an acrylic render finish to the sides and rear. The walls to the façade at ground floor level were insulated externally with 150mm expanded polystyrene and brick slip finish. (The difference in insulation thickness accommodated the brick slip thickness and brick cornice detail at first-floor level). Brick detailing, including the arch and projecting brick surround over the entrance porch, were replicated accurately from survey photographs with cut bricks. The projecting nose of the existing concrete cills were cut and over-clad with powder coated metal cills with a thin insulation board layer to reduce the cold bridging effect at this detail. The window reveals were insulated with a thin insulating board to finish within the depth of the frame of the existing window (which were retained in their existing position within the wall). The porch soffit and side walls were left uninsulated as the insulation thickness would have had an unacceptable visual impact on the stained glass entrance screen. This area is therefore a cold bridge with disproportionate heat loss compared to the insulated walls. See chapter 7.5.4 - porches, recessed porches & wind lobbies, in relation to this generic issue. Similarly, the walls of the unheated garage were not insulated externally or internally to the walls adjoining the hall & kitchen. Ideally, the insulation should be extended to these heat loss walls of the main house as they adjoin an unheated space. |
High Significant level of intervention. See paragraph below - Impact of Works on the Architectural Heritage
|
Attic Insulation |
The existing attic quilt insulation was topped up to a 300mm depth. Where the wall insulation was carried up to the existing eaves soffit, care was taken to ensure that the attic insulation overlapped the soffit at this point to avoid thermal bridging. |
Low All original fabric was retained |
For further information, see section on Attic insulation [link to follow] and the section on External Wall Insulation which further explores the question and issues relating to the over-cladding of existing houses with external wall insulation [link to follow].
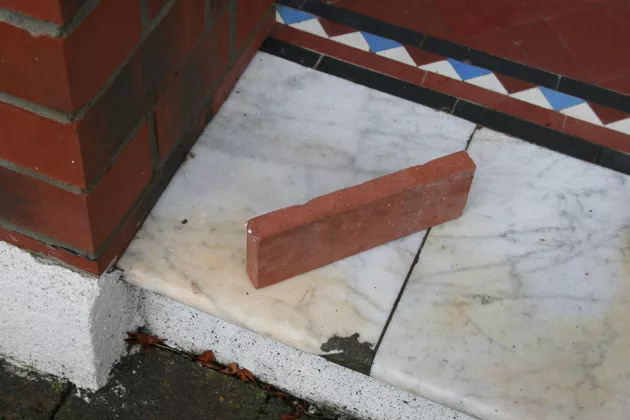
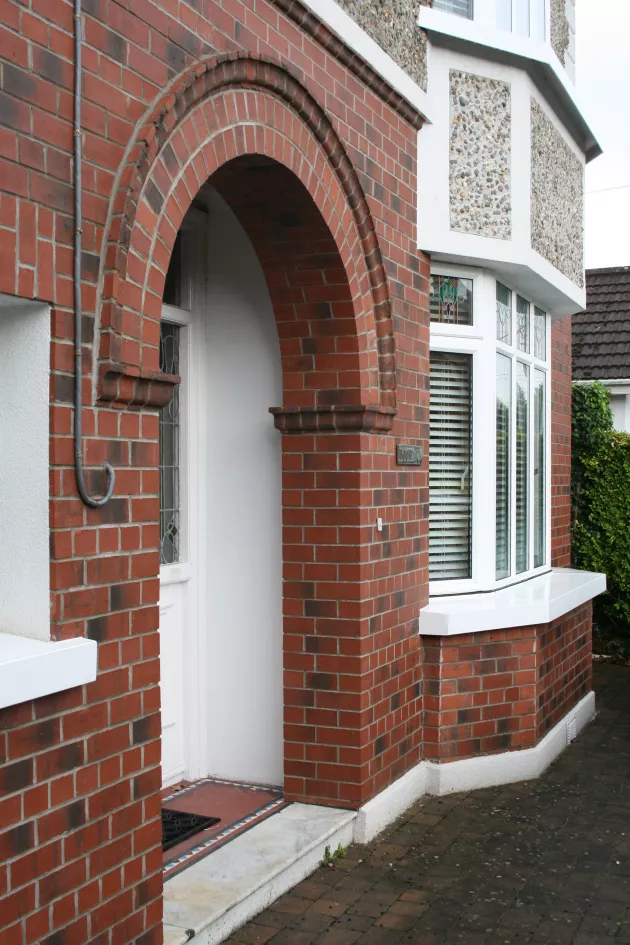
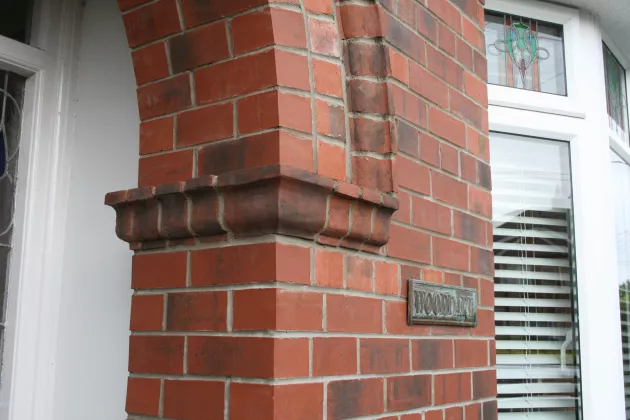
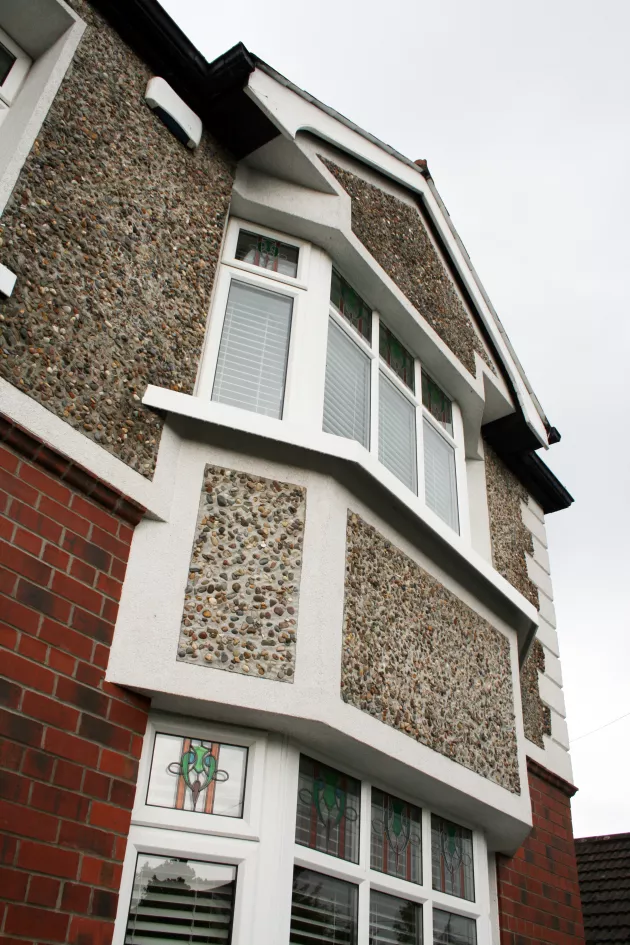
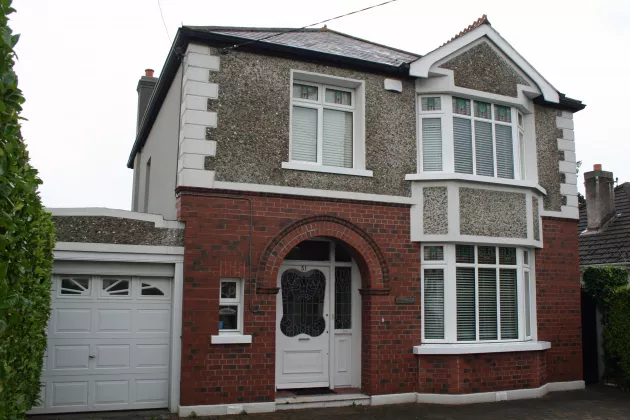